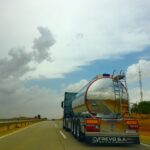
Dimensionnement en fatigue des véhicules et équipements embarqués
Mots clés : réservoir composite de stockage hyperbare de l’hydrogène, véhicules à pile à hydrogène, véhicules commerciaux (utilitaire léger, camion de poids moyen et lourds), sécurité, crash, fatigue, durabilité, simulation éléments finis.
Enjeux et objectifs
Le frein majeur à la démocratisation rapide de l’hydrogène au travers des moyens de transport reste les surcouts du véhicule à l’achat mais également de l’hydrogène lors de la recharge. Les batteries et l’hydrogène constituent deux briques technologiques complémentaires. Couplées, elles permettent de répondre à un large type d’utilisation en paramétrant la capacité des batteries, la puissance de la pile à combustible et la capacité des réservoirs à hydrogène (architectures possibles : range extender, mid-power, full power).
Un des facteurs clé du surcoût du véhicule hydrogène se trouve dans le stockage de l’hydrogène. Dans une démarche d’allègement, les réservoirs métalliques (type I et type II) ont laissé place aux réservoirs composites.
L’enjeu du dimensionnement en fatigue est important car il permet à la fois d’optimiser le système complet pour obtenir le meilleur compromis entre allègement et fiabilité, en respectant les critères existants ou les exigences associées à l’architecture du véhicule.
La méthodologie développée par nos équipes intègre les savoir-faire dans le domaine des essais de caractérisation en fatigue des matériaux ainsi que la connaissance des sollicitations mécaniques et vibratoires appliquées à ces systèmes.
Ces deux aspects contribuent à l’optimisation des simulations afin d’assurer une corrélation essai / calcul et permettant d’estimer la durée de vie optimale du système en amont des essais.
Ξ Systèmes et composants embarqués
Lors des chargements thermomécaniques cycliques, les réservoirs de type III sont limités par le matériau du liner. Quant aux réservoirs de type IV, leurs liners sont moins impactés par la pression, ils sont en revanche sujets au fluage et au phénomène de vieillissement du polymère.
Ξ Supports de maintient et retenue (Brackets)
Les sollicitations auxquelles ces systèmes sont confrontés doivent être connues pour effectuer l’analyse en fatigue. Ces dernières sont totalement dépendantes du choix de l’intégration du système dans l’architecture du véhicule.
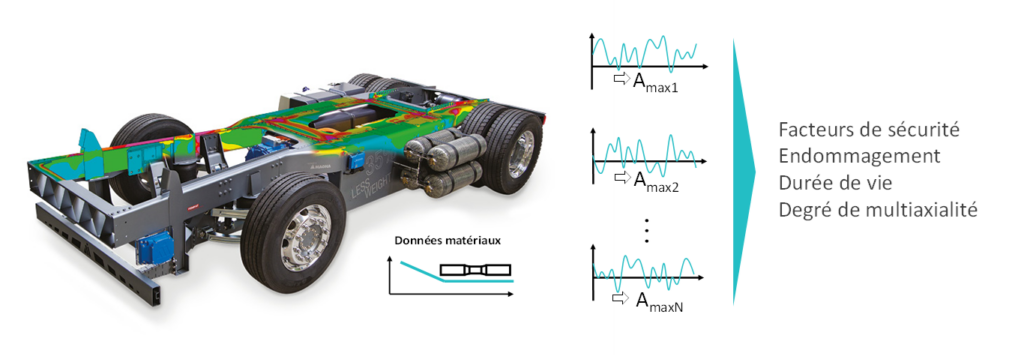
Prestations CIMES
Ξ Validation par calculs et essais de la tenue structurelle de réservoirs et systèmes de retenu (Bracket) composites
Ξ Optimisation du procédé d’enroulement filamentaire (géodésique, non géodésique, delta axisymétrique)
Ξ Minimisation de la masse et des coûts d’industrialisation avec respect des contraintes de tenue thermomécanique
Ξ Développement de méthodologies de validation interne et d’analyse en fatigue
Ξ Support pour le dimensionnement des liaisons châssis par optimisation multidisciplinaire
Ξ Caractérisation des matériaux (comportement thermomécanique, courbes S-N, comportement au fluage)
Ξ Mise en place et qualification des essais en sous-systèmes
Ξ Evaluation des ruptures de fibres/interfibres et du phénomène de délaminage
Ξ Modélisations avancées des équipements clés
Ξ Identification des spectres de chargements (conditions réelles, piste d’essais, modélisation multi-corps)
Ξ Evaluation des niveaux d’endommagement et définition des facteurs de sécurité