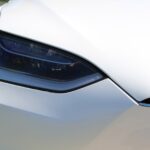
Optimisation multidisciplinaire de caisse en blanc automobile
Mots clés : caisse-en-blanc, allègement matériaux, optimisation multidisciplinaire, robustesse, cluster haute performance de calculs, automatisation de procédés, surface de réponse, méta-modèle, sécurité, crash, durabilité, NVH, simulation éléments finis.
Enjeux et objectifs
Les autorités européennes mettent d’ores et déjà une pression progressive sur le secteur automobile en imposant des niveaux d’émission de CO2 stricts. En conséquence, les constructeurs doivent s’engager à respecter un niveau de 95g CO2/km sachant qu’en 2018, la moyenne en Europe était de 120.5g CO2/km. Si les solutions de motorisations alternatives (hybride ou électrique) sont en pleine expansion, l’allègement des véhicules est également une voie permettant de réduire les émissions de CO2, on estime ainsi qu’un gain de 100kg induit une réduction de 10g de CO2/km.
Cela permettrait d’inverser la tendance qui a conduit à une augmentation continue de la masse des véhicules ces dernières décennies, notamment liée à l’augmentation des niveaux de performances requis en termes de sécurité, confort, qualité, conduite et habitabilité. On comprend l’importance de la simulation numérique pour les projets réunissant une multitude de contraintes de conception. En outre, les solutions de calculs permettent de dimensionner au plus juste les structures.
Ainsi, l’amélioration des solutions existantes se fait progressivement en prenant en compte les préconisations de chaque discipline (crash, NVH, …).
Dans une démarche d’amélioration technologique continue, nos équipes proposent de repenser cette optimisation multi-physiques manuelle en qualifiant une méthode permettant de traiter le problème dans son ensemble et prenant en compte toutes les contraintes dans la recherche de solutions. Grâce à l’automatisation, le temps gagné par les ingénieurs calcul sera réinvesti sur une définition réfléchie du problème d’optimisation (variables, cas de chargement, objectifs et contraintes) ainsi que sur l’analyse et l’exploitation des données générées par l’optimisation. Cette méthode permettra donc d’utiliser au mieux les ressources de calcul disponibles. L’objectif est de répondre aux nouvelles exigences du monde industriel, soient :
Ξ La réduction des temps de développement
Ξ La réduction des coûts
Ξ L’amélioration des performances
L’optimisation systématique permet d’orienter la conception vers une solution satisfaisant toutes les prestations tout en minimisant le coût et la masse du système évalué.
Prestations CIMES
Ξ Optimisation multidisciplinaire pour l’allègement de caisse en blanc automobile
ΞDéfinition de problème d’optimisation : espace de conception, cas de charge, objectifs et contraintes
Ξ Qualification de DOE (Design of Experiments)
Ξ Automatisation des procédés de calculs et optimisation des temps de calculs sur cluster HPC
Ξ Analyses de données générées par les optimisations
Ξ Prestation et analyses aux crash (sécurité passive) comprenant le respect de l’ensemble des critères liés à la sécurité des occupants du véhicule et des piétons
Ξ Prestation et analyses NVH, en charge de la validation du comportement vibratoire et de l’ensemble des rigidités de caisse (raideur globale en flexion, raideur globale en torsion, raideurs locales stratégiques)
Ξ Prestation durabilité, en charge de la validation du comportement en fatigue
Ξ Coordination interne des expertises métiers