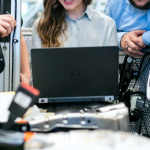
Qualification des niveaux de sécurité des véhicules à hydrogène
Mots clés : réservoir composite de stockage hyperbare de l’hydrogène, véhicules à pile à hydrogène, véhicules commerciaux (utilitaire léger, camion de poids moyen et lourds), sécurité, crash, fatigue, durabilité, simulation éléments finis.
ENJEUX ET OBJECTIFS
Depuis sa création en 1989, notre bureau d’études cultive un haut niveau technique dans le domaine de la simulation numérique multi-physiques. En parallèle de nos activités de simulation numérique, nous sommes en mesure de proposer une large gamme d’essais physiques (sous système et véhicule complet). Grâce à cette expertise, nos équipes ont pu développer des relations fortes avec les principaux acteurs de la mobilité (automobile, camion et ferroviaire). Aujourd’hui, nos investissements se focalisent sur des méthodologies innovantes de validation permettant de réduire les temps et coûts de développement.
Les solutions de mobilité douce commencent à fleurir au fur et à mesure du durcissement des normes anti-pollution sur les rejets de particules et du déclin annoncé des motorisations thermiques. Les véhicules électriques font l’objet d’un grand nombre de recherches pour accélérer leur déploiement et réduire leur coût. En Europe, l’accent est mis sur le développement de la filière hydrogène sous tous ses aspects (production, stockage, transport, distribution, application mobile) afin d’en conserver la maitrise technologique.
Un véhicule hydrogène est un véhicule électrique utilisant une pile à combustible pour transformer l’hydrogène stocké à bord en électricité afin d’alimenter en énergie le moteur. Par rapport à un véhicule électrique à batteries, l’hydrogène possède les avantages suivants :
Ξ Autonomie supérieure
Ξ Temps de recharge plus court
Ξ Densité énergétique supérieure (masse et volume)
Les freins majeurs à la démocratisation rapide de l’hydrogène au travers des moyens de transport restent les surcouts du véhicule à l’achat mais également de l’hydrogène lors de la recharge. Les batteries et l’hydrogène constituent deux briques technologiques complémentaires. Couplées, elles permettent de répondre à un large type d’utilisation en paramétrant la capacité des batteries, la puissance de la pile à combustible et la capacité des réservoirs à hydrogène (architectures possibles : range extender, mid-power, full power).
PRESTATIONS CIMES
Ξ Validation par calculs et essais de la tenue structurelle de réservoirs et système de retenue (brackets) composites
Ξ Optimisation du procédé d’enroulement filamentaire (géodésique, non géodésique, delta axisymétrique)
Ξ Minimisation de la masse et des coûts d’industrialisation avec respect des contraintes de tenue thermomécanique
Ξ Développement de méthodologies de validation interne et analyse au crash en fonction de l’architecture véhicule
Ξ Support pour le dimensionnement des liaisons châssis par optimisation multidisciplinaire
Ξ Transcription des normes et règlementations (ECE-R100/02, ECE-R134/02, …)
Ξ Mise en place et qualification des essais sur véhicules complets et sous-systèmes
Ξ Evaluation de l’incidence de la sécurité passive dans le développement et l’intégration des équipements
Ξ Modélisation avancées des équipements clés
Ξ Optimisation des systèmes de retenue et de protection
Ξ Evaluation de l’intégration des équipements et des risques associés